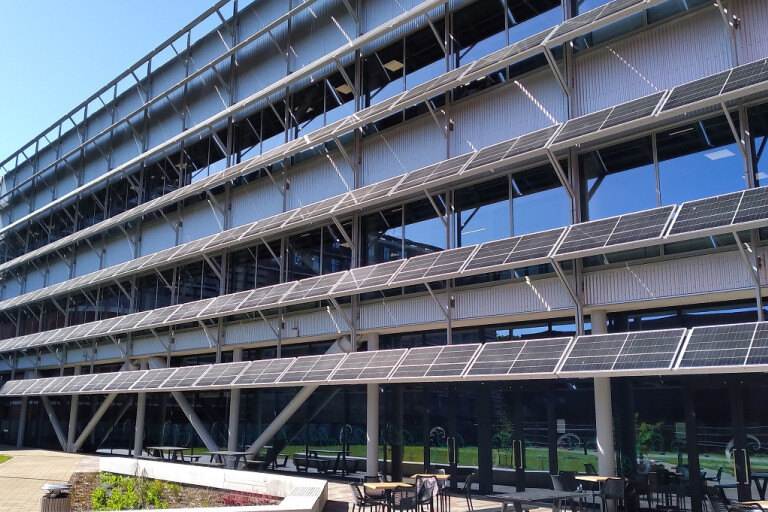
TECTONUS DMAX
REDUCE DEMAND / MAXIMIZE SAVINGS
With high damping and low overstrength factor, DMAX braces allow engineers to downsize their structure, unlocking significant cost savings in structural members, connections and foundations, and freeing up usable space. Ultimately DMAX provides a stronger, safer and more efficient building to the delight of owner and occupier.
Straight Swap for BRBs, EBFs, CBFs
Tectonus DMAX is a steel brace supplied end to end, with some unique advantages compared to other bracing systems:
- Elastic Perfectly Plastic hysteresis
- Very high damping (>50% in some cases)
- Best-in-class Overstrength Factor - 1.15
- No replacement post-earthquake
DMAX incorporates the well-proven Tectonus DFFJ friction damper.
Value Engineering Opportunity
Tectonus DMAX delivers unmatched value on braced frame buildings in seismic areas:
- Comparable price to BRBs
- Up to 50% savings in structural actions
- Reduced members sizes
- Reduced foundation works
- Reduced connections and detailing
- Increased useable space.
Savings across structure and foundations have been demonstrated to more than pay for the cost of DMAX braces themselves.
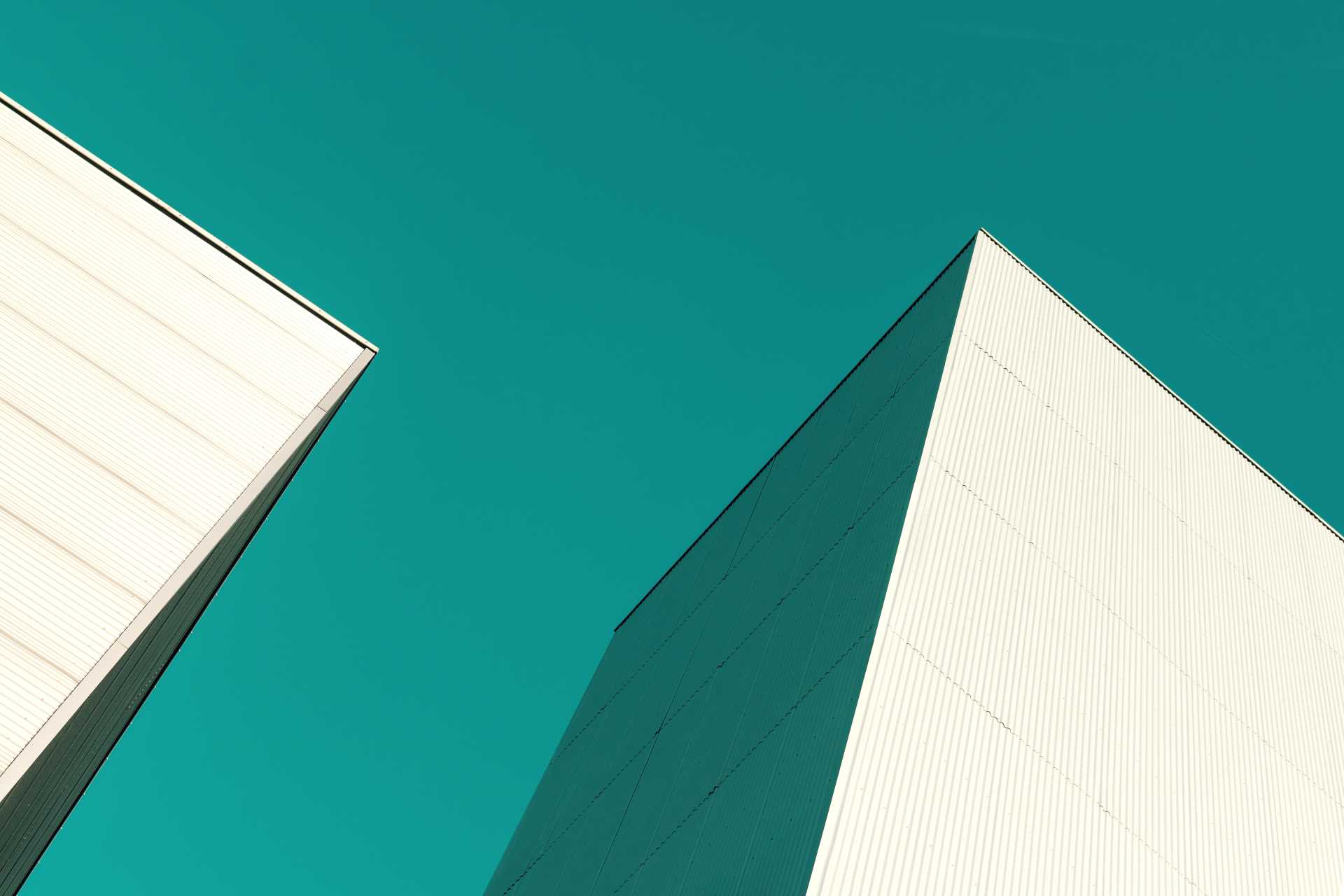
"With comparable pricing to other lateral systems like BRBs, the DMAX system’s high effective damping and lower overstrength factor have allowed us to achieve significant cost savings across the entire lateral system, including braces, columns, diaphragms, and foundations."
Stable E-P-P Performance
- Any load and deformation capacity is possible
- No limit to maximum deformation
- Multiple units in parallel can be used for large force demands
- Configurable (size and no.) to the design level earthquake
- Built-in anti-buckling mechanism
- Every damping unit is performance tested.
DMAX has been tested to ASCE 7
- DMAX brace was tested according to ASCE 7 at AUT Structures Lab
- Prototype tested against OSHPD/HCAI protocols in a 17025-certified US lab
- The DFFJ damper has been component tested according to ASCE 7-16 loading protocols
- Reports are available upon request.
Constructability
- Pre-shipment, every brace damper is individually performance-tested
- Tolerances better than AISC approved 1/32”
- Length adjustment by shimming during installation
- Lower weight due to hollow section – no concrete filling
- SHS sections can fit within standard wall profiles
- Braces come primed and ready to paint according to the required paint scheme
How it works
DMAX is a steel tension and compression brace supplied end to end.
The brace incorporates Tectonus DFFJ friction damper technology and a proprietary mechanism to control global buckling.
In an earthquake, energy dissipation is provided by controlled sliding of the friction surfaces. These surfaces have a proprietary surface covering to ensure stable performance across a range of frequencies— and pre-tensioned disc springs to adjust the clamping force.
There are no yielding components, allowing DMAX to perform through multiple earthquake events. There is nothing to replace post-earthquake.
Project Feasibility
To quickly assess project feasibility, replace the BRB or other brace element and use the following factors for DMAX:
- Ductility R=8 (US) / RdR0=4.8 (Canada) / Mu=3.5 (NZ)
- Overstrength (capacity design factor) of 1.15
Worked Example
For example, taking a 1000 kN BRB which has an overstrength factor of 1.6 - 2.5 and replacing it with a 1000 kN DMAX brace with overstrength of 1.15 means the capacity design of the connections, members, and foundations can be downscaled from 1600-2500kN for the BRB example to 1150 kN for DMAX. In our experience, given that DMAX and BRBs are the same price, the force reduction can translate into significant construction cost savings.
Modelling Guidance
Typically the DMAX ductility factor can be improved through further modeling and analysis (involving nonlinear time history analysis).
To model DMAX braces, follow these instructions:
- In ETABS and SAP2000, use ‘Plastic-Wen’ Link element
- In PERFORM3D, use an ‘Inelastic Bar’ element with E-P-P properties
For further modeling guidance, please check out the following video tutorial.
If at any stage you need help please don't hesitate to get in touch.
Get in touch to schedule a no-obligation discussion about your project.